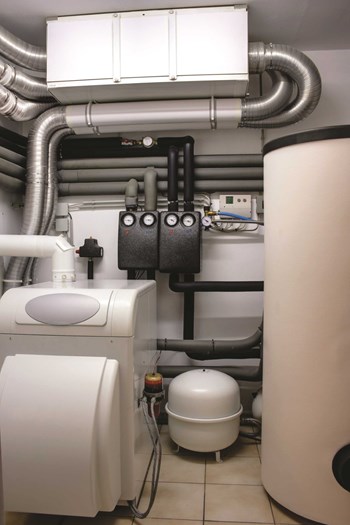
The rarely stated—but all too well understood—Murphy’s Law for Boilers—asserts that if your boiler quits working, it will do so on Christmas or New Year’s Eve, or at 4:45 p.m. on the coldest day of the year. With some planning, though, that broken-down boiler won’t be yours on those inopportune frigid days. An association’s management and staff can head off a worst-case scenario by scheduling regular maintenance and keeping an educated eye on the whole system.
With the heating season in Chicago extending from October to May, being certain that your building’s boiler will function well should be a high-priority concern for the building’s management. Maintenance also saves money by improving efficiency and extending the useful life of mechanical equipment.
Maintenance Musts
Michael Then, marketing manager at ABC Plumbing, Heating, Cooling & Electric in Buffalo Grove says that “general year-round maintenance varies,” and depends on whether the boiler is providing domestic hot water and heating, or just heating. “If the boiler provides both, then the unit should be inspected twice per year. If it's only providing heating, then once a year is sufficient,” Then says.
“Essential inspection items include but are not limited to: testing safety switches and relief valves, inspecting and lubricating pumps where applicable, checking exhaust venting to make sure it's in proper working condition, pulling, cleaning and inspecting burners and always following manufacturer inspection and maintenance procedures,” says Then.
When Extra Care is Needed
'Regular servicing' can mean different things for different boilers. The need for more frequent maintenance and cleaning depends largely on the particular system—whether it's oil or gas, steam or hot water, large or small, old or new, steel or cast-iron.
For example, oil burners need more frequent cleaning than those that run on natural gas. A major cleaning is an 8- to 10-hour process, and the boiler must be shut off and allowed to go cold first, which is why it makes sense to do a major cleaning before the heating season starts. On the other hand, a supplementary cleaning can be done while the boiler is still operating, and typically costs about half the price of a major cleaning. Experts recommend that No. 2 oil-burning boilers have supplementary cleanings at least two or three times during the heating season, in addition to the major cleaning. A building with a boiler that’s burning dirtier No. 6 oil should have an outside company come and clean the boiler monthly during the heating season.
According to Bronson Shavitz of Shavitz Heating & Air Conditioning in Skokie, “Steam boilers always need more maintenance and safety testing. Most steam boilers have a recommended schedule that includes weekly visual inspections, weekly blow-down or draining of low-water cutout safety devices, monthly component inspections, and annual full-system tune-ups.”
“Larger boilers may require more maintenance per manufacturer’s specifications,” he continues. “Older boilers need to be inspected more often due to the potential for worn-out parts to fail and the lack of safety devices compared to today's standards.” Shavitz adds that steel (as opposed to cast-iron) boilers also need chemical treatments for the water, and that chemical servicing should be done monthly during the heating season.
Spotting Trouble
While much of the work needed for a boiler is done by outside companies, some things can be accomplished by a building or association's superintendent, or another staff member tasked with the job. Properly maintaining a boiler isn’t just checking the machine from time to time and responding to emergencies; it’s about being vigilant.
“Building maintenance staff and supervisors should perform regular visual inspections for any leaks, noises or unusual operation,” Then says. “Daily maintenance should be done with a visual inspection and walk-through of the mechanical equipment.”
Your superintendent or chief engineer should monitor the daily intake of water into the system by checking the water meter. Check the stack temperature every day to see that the temperature is not elevated above normal. Check for leaks. Indications of leaks might be condensation, wet spots on equipment or the floor (in the case of heating lines buried in the floor), or obvious dripping of water from the system. In addition, the super should monitor the fuel strainer, which can have residue buildup that will affect the system’s efficiency.
And just as your average motorist knows more or less how his or her car sounds when it’s running properly, the staff member tasked with monitoring your boiler should have an ear for the building’s heating system. “Get to know what normal operation is by watching and listening to the equipment while the professional is on site,” suggests Shavitz. “Then watch it and listen to it regularly. If anything looks or sounds different, get the professional in to check it and repair as needed.”
All that being said, Chicago gets mighty cold—and sometimes when it comes to keeping the heat on, a walk-through by even a very competent custodial staff member isn't always sufficient. The city requires an on-site engineer for large boilers. According to Sid Watkins of Murphy & Miller in Chicago, “If you're only a two-flat, that's one thing. If you're a high-rise, you should have an engineer that's taking care of the building. In downtown Chicago high-rises, you typically have building engineers. Building engineers will walk through—some of them do it daily, some of them do it weekly—and will check the safeties of the boiler, if it's a steam boiler, to see if the water cut-off is working. They'll make sure that everything is working properly. They will also make sure that the chemistry of the boiler is where it should be. They work with the water-treatment company to make sure that is maintained so that you do not do damage to the boiler or the piping.”
Whoever is in charge, signs of trouble—however small—should never be ignored. A quick phone call to the service company could alert the super or engineer to the need to shut down the system to avoid big-time (and big-ticket) problems.
Possible Disaster
And there's more at stake with boiler care than just the risk of a chilly night or two, warns Shavitz. “There are numerous documented cases of boilers in schools, condos, apartment buildings and factories where boilers caused fires, explosions, and/or carbon-monoxide poisonings due to neglected and/or improper maintenance. These cases have led to severe building damage, injuries, and even the deaths of many people. Unfortunately, you can Google boiler explosions or boiler carbon monoxide and find more examples than you would care to know about.”
Watkins tells of a situation he walked into with a customer, where, he says, “the boiler was dumping burning soot out of the drains. And if that wasn't bad enough, it was spewing that burning soot on top of the gas supply to the boiler. The building was unoccupied, and there was nobody there to monitor it. Something happened during the course of the previous winter, and it sooted up. We were there to do a fall start-up of the boiler and get everything running. It was a very dangerous situation. That was a time bomb waiting to go off.”
Legally Speaking
“Illinois law,” says Then, “requires all boilers be registered and inspected when situated in locations frequented by the public or buildings having more than six dwelling units. Per the state's fire marshal guidelines, inspections are required at one-, two- or three-year intervals, depending on the type of equipment. High-pressure boilers require internal inspections annually. Low-pressure boilers typically used for heating and supplying potable hot water are inspected every two years. Pressure vessels are required to be inspected every three years. Shavitz adds, “Many municipalities also have required inspections for commercial boilers that vary greatly.”
Although conversion to cleaner-burning oils or natural gas hasn't been mandated in Chicago as it has in some other major cities, many boards have decided to switch to gas due to environmental concerns and the lower cost over time. Currently, natural gas is cheaper to buy, and because it's more efficient, less expensive to run. It requires fewer regular service visits as well. The two types of systems aren’t the same, though, and require different maintenance. Failure to notice warning signs of trouble, especially with a natural-gas system, could be disastrous, so re-education of all staff members who are ever responsible for the boiler is critical.
A boiler should work well for decades. Just how long it lasts depends partially on its construction and how it was installed—but mostly on how it is maintained, so boards and managers should avoid being penny-wise and pound foolish. Calling on your professional maintenance service more often than strictly necessary can extend the life of your expensive-to-replace boiler. “There are so many different things that can fail due to improper maintenance and result in expensive repair bills,” Shavitz says, “that regular maintenance is a money saver. Think how much more expensive replacing your car's engine would be if you chose to 'save money' by not changing your oil. Add to that the typical three- to ten-percent energy savings that can be expected from a proper maintenance and cleaning, and you can see that it typically costs more money to not maintain the equipment.”
Sooner or later, though, even the best-kept system, or elements of it, will conk out. “The silver lining of when those components do fail is that it gives the building an opportunity to upgrade them to energy-saving systems,” Shavitz explains, “which can end up paying for themselves quite quickly since as we all know, winters in Chicago are neither short nor mild.”
Jonathan Barnes is a freelance writer and regular contributor to The Chicagoland Cooperator. Staff writer Judy Hill contributed to this article.
Leave a Comment