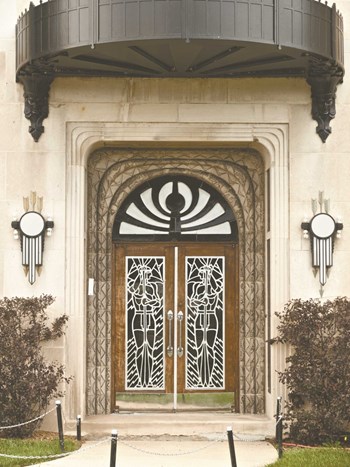
For those who might not know, building facades are the exterior walls of a building—they're important not just for their architectural and aesthetic significance, but because they're built to withstand the elements and preserve the underlying structure.
According to Steve Gallagher, directing manager of Tractel Ltd.’s Swingstage Division, facades are usually attached directly to the frame of a building, but some can also be welded or embedded.
Material Culture
Brian Hauschild of Apex Exteriors Inc. in South Elgin says that there are many types of facades found in Chicago area buildings, including vinyl siding, cement fiber board, aluminum, cedar, stucco, and systems like Exterior Insulation and Finish Systems (EIFS) covering, often called foam siding.
Some materials are more popular than others, of course. Hauschild says that many builders have gradually moved away from aluminum siding because of its high cost and limited durability. “It bends fairly easy, and people are going to newer products like vinyl that look more natural and cost less,” he says. “Insurance companies also want to stay away from aluminum due to hail storms and other risks.”
Types of building facade can also vary with the level of pricing of a home. Many homes throughout the Chicagoland area are built using vinyl as the structure’s primary facade material.
“More or less with vinyl it’s in the houses in areas that may fall into medium-priced homes,” Hauschild says. “Cedar, cement fiber and stucco are more custom to higher-medium to higher-end priced homes.”
This has not always been the case with homes built in the greater Chicagoland area, however. Hauschild says that early on, more high-maintenance materials—such as brick and wood siding—were commonly used in buildings and homes. Also trends in durability have prompted homeowners to utilize materials that are both cost-effective, durable in varying weather conditions and easy to maintain over a period of time.
“Vinyl siding or cement fiber board both have very little maintenance and can last about 30 years,” Hauschild says. “Cement fiber board can give you the look of original cedar, but with a longer warranty and much less maintenance.”
In more commercial and industrial projects, Sergey Taitler, general manager of All American Exterior Solutions in Lake Zurich, says that brick and cement tended to be commonly-used materials for exterior facades. However, the industry is now moving towards composite fiber materials such as Trespa facade systems. Also common is the use of insulated metal panels, which enable builders to make a wider variety of shapes, colors and forms.
“I see a lot of buildings in the city with these metal facades, they look more futuristic,” Taitler says. “That’s what these buildings are going to because architects can now make more differentiated forms and designs than they can with brick, pre-cast or concrete.”
The Letter of the Law
As far as Chicago building codes, Chicago has a similar code to many international building codes—though suburban areas have their own perspective building codes, which can vary for facade maintenance contractors working between different suburbs.
“Most municipalities just follow International Building Code but some can be more stringent,” Hauschild says.
Building codes can also vary based upon where a municipality is located. “It’s all dependent upon the area and what the village wants,” Taitler says. “Some have certain wind uplift gradings, mainly so that when the Chicago winds blow through, the facade won’t blow off.”
Usually local authorities inspect a building’s facade, but also the Occupational Safety and Health Administration (OSHA)—a division of the U.S. Department of Labor—inspects buildings to ensure that their facade is safe for both owners and contractors.
“It’s more regulated in states like New York and California," says Gallagher. "There, they have to meet specific OSHA codes such as 1910-66, ANSI I-14."
The ANSI/IWCA I-14 is an American National Standard published in 2001. The intent of the I-14 Standard is to improve the level of safety in the window cleaning and exterior maintenance industry. The 1-14 Standard provides safety guidelines that benefit building owners, managers and contractors. Safety in the workplace is a shared responsibility; by following the voluntary I-14 Standard, both lives and assets are protected. The standard concerns scaffold safety and explains the shared responsibility for building owners/managers and contractors doing exterior construction and maintenance while working at certain heights. He adds that regulations can also be dependent upon how tall the building is. “At a certain height, the platform has to be supported with certain codes,” he says.
Chicago’s building ordinance applies to all buildings with exterior walls that are 80 feet or more in height. The code includes “critical examinations,” which building owners are required to have every four, eight or twelve years depending on the building classification.
Additionally, building owners are expected to have an ongoing inspection—which occurs at the halfway point of the critical examination cycle—to report to the city that the building’s structural facade is still safe.
In addition to following building codes, many jobs require a permit from the municipality as well as a certificate of insurance from the contractor.
“Depending on where you’re doing the work, most of the jobs require a permit,” Hauschild says. “Sometimes they don’t, but in the process, they may ask what you’re doing and the steps you’re doing to do that process. Most companies have to be registered in municipality that they’re completing the work in.”
Some Things to Consider
Chicago is an old city boasting some world-renowned architecture. But with that age and beauty comes a lot of costly maintenance. Many Chicago clients are often tasked with making tough capital expenditure decisions with respect to their facades, notes Helios Design +Build, a development, construction management and consulting firm. Here are some important points for exterior facade maintenance projects:
• What’s your timeline? – Most products you might use on your façade (joint sealant, masonry sealer, mortar, etc.) require at least 24 hours with a temperature not to drop below 35–45 degrees Fahrenheit. As a general rule of thumb for Chicago, plan to be done with your project no later than November 15th to avoid issues with cold weather.
• What’s included in your contractor’s schedule? – Have they specified calendar or business days? Have they accounted for holidays? Have they accounted for potential inclement weather days or will those be added to the schedule as they occur?
• How much work needs to be done?– The city needs to know how much work will be done to your façade, including details like lineal footage of lintels to be replaced and square footage of bricks to be repointed. They will use these estimates when calculating your permit fees.
• Do you qualify for the Façade Rebate Program or Small Business Improvement Fund?– The City of Chicago provides money to property owners in certain locations who meet certain criteria through the Facade Rebate Program and SBIF. Mark your calendars for the next application period.
• How will this work affect tenants and residents?– While the majority of facade work will, obviously, be done on the exterior of the building, there are a number of items that might require interior access and work that will surely disrupt your unit owners/tenants. Plan accordingly and coordinate with your boards/residents.
• Plan to hire an experienced (and insured) pedestrian canopy contractor?– Falling debris is not to be taken lightly. Make sure you have appropriate protection for pedestrians and that your contractor follows OSHA safety guidelines.
Permission to complete a job can also be dependent upon the materials being used in a project because of Chicago’s varying weather conditions.
“We’re trying to protect from wind uplift,” Taitler says. “Chicago has lots of wind, snow and rain, and often times the architect has certain specifications that the engineer has to approve are correct to withstand weathering.”
However, special landmarked facade treatments require contractors to have a certain level of certification prior to installation. James Hardie, a building products manufacturer for over 100 years and a cement fiber siding company, is among one of the producers that requires contractors to receive this sort of certification.
Hauschild says that there is also a Vinyl Siding Institute that contractors can receive their certification from. Many products have strict programs. “There’s a vinyl siding institute where you can become certified to install the products, and you’re basically taught and tested on it,” he says.
Regardless of the grade and pricing of the product that is chosen, the strength and safety of the materials are of the utmost importance in Chicagoland’s changeable winds and weather. n
Rosie Powers is a freelance writer and reporter living in Chicago.
Leave a Comment