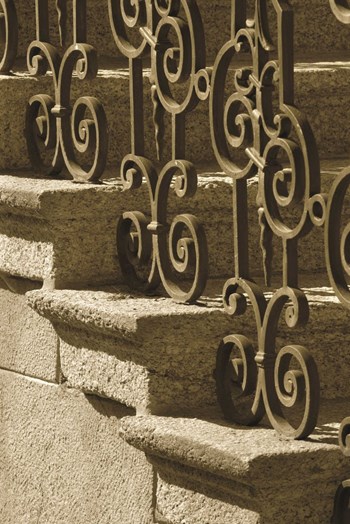
After one cursory glance through the streets of Chicago, the reason becomes clear as to why The Windy City is well-recognized, architecturally, as a city of innovation. After the Great Chicago Fire of 1871 ravaged many downtown properties, buildings that reflected the more classic aesthetic of New York and Boston at the time were demolished, replaced by the city’s fabled skyscrapers, immortalized by William LeBaron Jenney's Home Insurance Building in 1895.
James Collins, AIA, NABIE, LEED AP, the president of Criterium-Collins Architects & Engineers in Oak Park, pinpoints the 1880s as a turning point in Chicago architecture, when stonework became more prevalent, and designers left their marks through carvings. This was replaced by terracotta in the 1920s, according to Collins. “Iron work was never that popular around Chicago, in regard to decorations and what-not,” he says.
Metal work, however—ornamental and otherwise—still had (and has) a place in the city’s architecture. Whether via subtle touches (i.e., rails, cornices, gutters and busts, or outwardly exposed steel and aluminum structural work), those with a keen eye can spot metallic touches, both new and old, that reflect both the city’s past and future.
Metal work comes with a certain level of responsibility. Rust and decay can turn a shiny and vibrant, eye-catching addition to a property into a rusty albatross if not properly maintained, as the city’s infamously aggressive winds and weather bare down on a building’s various metallic instruments. With a careful touch and a commitment to maintenance, though, some flashy metal accoutrements adorning a property can provide a welcome respite amid a city crafted mainly from stone or brick.
Metal Detecting
While rarely the predominant exterior feature in Chicago co-op and condo properties, metal work can be spotted throughout the city's many unique neighborhoods. While types vary, steel maintains the top spot as the most frequently implemented, according to Rob Mueller, president of Mueller Ornamental Iron Works, Inc., in Elk Grove Village. "Especially in regard to ornamental metal decorations, years ago they were all made with sheet metal or cast iron," he says.
"Most of the various neighborhoods have a good percentage of metalwork in them, so it would be hard to say which area leads the pack," Mueller explains. "I wouldn't say that there are any standouts, and that it's pretty equal across the board."
Dan Baigelman, AIA, an architect with Full Circle Architects, LLC in Highland Park, cites gutters (somewhat surprisingly) as the example of ornamental or decorative metal work that he has encountered most often while plying his trade in Chicago. Often, architects—predominantly those of the 1920s—would adorn the cornices of gutters with more charming flourishes, a clever way to add a little artistry to a less glamorous, but very necessary, furnishing. Many of these metallic gutters were implemented in the now-vintage, 15-story to 20-story skyscrapers that adorned the lake, according to Baigelman. Nowadays, he says, there are still some 100-year-old houses that preserve this aesthetic, but the taller buildings have switched to cheaper materials, which are easier to maintain.
Collins, on the other hand, points to metal railings as the predominant frontrunner for this type of architectural feature in The Windy City. "Looking back at the older buildings and thinking on those, railings are really the standout," he says. "In the old buildings, they were cast iron, and in the newer buildings, they're either steel or aluminum. The cast iron was used from the 1870s into the 1920s; beyond that, they went to steel railings, which were somewhat less ornate."
While he doesn't dispute Mueller's assertion that there's metal work throughout the city, Collins speculates that most of this architecture is located in the higher density areas, where multi-unit buildings reign. "The density signifies that there aren't as many large family units, with the occasional Juliet balcony providing the only outdoor space for residents. Some of these had ornamental railings in front," says Collins.
History of Metal Work
Chicago was in its infancy still as a burgeoning metropolis while East Coast cities like New York and Boston were thriving. Naturally, as the latter cities became significantly more crowded, entrepreneurs journeyed to the West; this matriculation had an effect on many of the city's industries, and architecture was not exempt.
As Collins sees it, much of Chicago's earliest architectural influence was an emulation of those styles popular in New York and Boston. "Much of our influence came from the East Coast, and—although for a short time—Chicago architects attempted to break out of that box, their styles never quite effectively caught on. People see things that they appreciate and think, 'I want something like that,' and this mentality let the East Coast drive much of early Chicago architecture."
The dual-pronged proliferation of both photography and train travel in the late 1800s allowed influences and styles to spread more easily and thus distant communities became more close-knit. "Styles were constantly evolving and changing, but I can't think of a single period of time that was governed by a single particular influence," says Collins, although he cites classic Greek and Roman styles—the latter personified by the work of Henry Hobson Richardson—as those with widespread impact.
When the Great Fire devastated much of Chicago's metal-heavy, classically—styled buildings in 1871, the aforementioned skyscrapers became the city's trademark architectural innovation. Ornamental metal made a comeback in the 1920s, when these towering structures were often constructed with high-sloped roofs, which were themselves adorned with decorative metallic flourishes including the gutters and cornices mentioned by Baigelman. Alas, this style was not long for the backyard of both the Bears and the Bulls.
As Collins explains, the high, hard-to-reach locations of these ornamental metal works rendered them easily ignored by property owners and management. They were easy targets for the elements, and fell victim to rust and wear. "Several prominent buildings had sheet metal cornices on the top. But most of those have disappeared as they've all more or less rusted away over time," he says.
Baigelman echoes Collins sentiment. "Because of their locations at the cornices of buildings, at roofs, at edges, ornamental metal installations were not easily maintained,” he says. “And because much of the work adorned gutters, they tended to deteriorate from the top, making it even more difficult to monitor their gradual decay.”
Given the high cost of fine metals, the idea of replacing these structures once they'd outlived their charm had just too high a price point. Eventually, the craftsmen capable of such work faded away, and the decorative works were replaced with cheaper metals.
"As there was less of a market for this type of work, the buildings themselves changed," explains Baigelman. "The high-sloped roofs were replaced by flat alternatives and the gutters by roof drains,” he says. “The older style just became too expensive to replace in kind."
Trying to Maintain
Those associations, managers, and owners whose properties do feature significant exterior metal work should make sure to inspect everything twice per year, ideally in spring and fall, for rust, peeling, cracks, deterioration, and other problems. Typically, any basic routine maintenance—such as repainting—can be done by a super or manager. More extensive repairs, however, should be left to a professional metalsmith, especially if the building is a historic property. As with anything, though, there's no one right way to approach upkeep; variables are always afoot.
"Frequency of maintenance depends on how the metal work was initially prepared," says Mueller. "It also depends on the company that produces it. Our steel typically provides property managers five to seven years before they'll have to do something. But if companies don't put adequate time and effort in, it can result in a situation where the homeowner may save money up front, but have to shell out more and earlier down the line, due to the fact that it wasn't prepared right in the first place.”
"Much of the maintenance simply involves someone touching up the work with paint once per year, but that again depends on the upkeep," Mueller continues. "If an association barely endeavors to maintain its metal work, it rusts away much faster, while those who keep a watchful eye end up with longer lasting material."
Nü Metal
While the former uses of ornamental metals have more or less petered out over the years, Chicago could be primed for resurgence, especially now that the recession is finally in America's past.
"There was a phase going into the recession wherein exposed structural steel was often used to give buildings a contemporary look," says Baigelman, although he speculates that, due to subsequent construction slowdowns and tougher energy conservation codes, this receded somewhat in the early 2000s. "It's difficult to build with that exposed steel right now, as it doesn't thermally stand up to current energy standards. That type of metal work is currently confined to canopies and the like."
However, as they say, where there's a will there's a way. Baigelman continues: "A lot of new buildings are using exposed metal in paneling, or curtain walls. This involves a thin sheet of metal masking rigid installation; it holds up to the aforementioned energy codes, and is becoming increasingly popular in new construction."
Mueller is equally optimistic. "Things do seem to finally be getting back to normal after the recession," he says. "They're starting to build again, especially in the commercial sector, which usually leads the way to residential."
Mike Odenthal is a staff writer at The Chicagoland Cooperator. Freelance writer Lisa Iannucci contributed to this article.
Leave a Comment