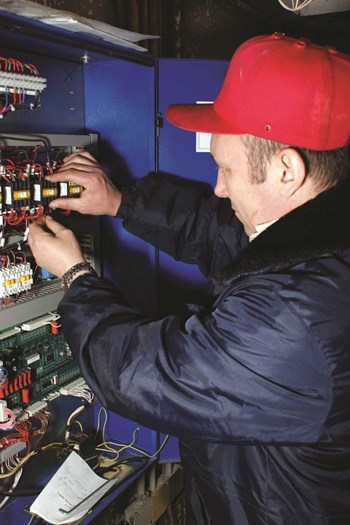
There are approximately 22,000 elevators and moving conveyances in the city of Chicago—and that number almost doubles when you add in the surrounding communities in Illinois. A great number of these elevators are in condominiums and it’s vital that those in charge understand the codes and maintenance that is required to keep them running smoothly.
Understanding the Differences
There are two basic kinds of passenger elevators used throughout Chicago’s residential buildings: traction and hydraulic. The latter is operated by means of a hydraulic ram, consisting of a piston mounted below the elevator inside a hollow cylinder and adjoined to an electric pump motor. The elevator rises when a liquid substance—usually oil—is pumped into the cylinder. To lower the elevator, the liquid is released from the cylinder by way of a valve.
The more expensive traction elevators are hoisted by a set of four to eight cables that are threaded over a grooved pulley known as the sheave at the top of the shaft and affixed to a counterweight that rises when the elevator descends, and vice versa. The sheave is turned by an electric motor; in gearless traction elevators, the motor is directly attached to the sheave, and in geared traction models, the motor is engaged to a gear train that turns the sheave. Since the counterweight weighs about as much as the elevator when filled to about 40 percent capacity, a traction elevator takes relatively little energy to operate.
“As technology goes, elevator improvements go at sort of a slow to medium pace,” says Rob Bailey, president of Mid-American Elevator, Inc. in Chicago. “There’s been changes in the computers and the motor drives that run elevators in the last 10 to 15 years, and an influx of foreign-made equipment that people need to stay on top of.”
Codes and Requirements
The American Society of Mechanical Engineers (ASME), with input from the Elevator Manufacturers Association of the United States, published the first safety codes for elevators and escalators in 1921.
According to Carl Byrd of the Chicago Department of Buildings' Bureau of Elevators, in the state of Illinois, someone who works on elevators needs to have proper certification and a license.
“They operate under elevator code, A.17.1, which is 350 pages of rules and regulations that all mechanics and maintenance workers must adhere to,” he says. “It is the mission of the Bureau of Elevators to inspect all elevators in our area in a timely manner.”
A number of elevator contractors in Chicago are union contractors with the International Union of Elevator Constructors (IUEC) and requirements for certification includes a five-year apprenticeship program that includes weekly classroom training and then five years of specified on-the-job training.
Qualified Elevator Inspector (QEI) is defined as a person meeting the qualifications, who is engaged in the inspection and testing of equipment within the scope of ASME A.17.1. This code covers the design, construction, operation, inspection, testing, maintenance, alteration, and repair of the following equipment, its associated parts, and its hoistways, where located in or adjacent to a building or structure. Continuing education is also required for most QEI inspectors.
ASME has a checklist that should be used by an inspector to determine code compliance to the effective codes for that specific elevator, and all components of the elevator need to be checked for compliance. Tests are required to be performed by elevator personnel and witnessed by a QEI certified elevator inspector.
Replacement Time
In today’s ever changing and highly competitive environment, building owners and property managers find that outdated elevator systems are a major reason for resident dissatisfaction.
“Advancements in technology have changed the way in which an elevator system functions. This perception has a direct reflection of the building itself,” says Ray Zomchek, president of Colley Elevator Co., in Bensenville. “Modernization will not only improve the aesthetic appearance of your interior and exterior, but will bring your elevator up to current city codes. Most importantly modernization of an older elevator unit will greatly improve performance and safety throughout your entire system.”
Elevator modernization includes updating of an elevator’s equipment to make it more reliable, bringing it up code compliance, reducing repair expenses and increasing the overall safety of the elevator system.
“The last thing anyone wants is for a resident to get stuck in an elevator,” says Shukarullah Malik, president of Pascal Elevator Company in Berwyn. “An elevator has a normal service life of about 25 years, so if your condo is utilizing a system that was put in place before 1985, the problems may become more serious. In older elevators, the control system—which can frequently mean the computer or motor drive—is becoming obsolete. Technology changes really fast so that computer is becoming a real antique and that is going to need to be changed.”
Vital as they are, it comes as no surprise that elevators are a huge investment. A typical new condo elevator, 20 stories, is $250,000 and up.
“If you take care of it and do the proper preventative maintenance, which would be maybe 2-3 hours a months, it will last 25 to 35 years,” Bailey says. “Price has become a huge issue on the marketplace the last three years, and everyone is looking to save money and scrimping on the maintenance. You may be saving money up front, but you may only get 15 years of service.
Maintenance Program
A first-rate elevator maintenance program for a 20-story elevator will normally run around $500 a month.
“Preventive maintenance is imperative,” Malik says. “An average elevator life span is 25 to 30 years, so it is important to keep the entire system in shape so that safety doesn’t become an issue. We list things that an owner should look for; if you hear strange noises, if you go to the machine room and you see stuff spewing red off the ropes, the grooves get worn out, the controller starts to smell funny, oil is leaking…these are things that can signal trouble.”
Typically elevator maintenance in condo buildings is called a full maintenance contract, which includes preventative monthly maintenance and any troubleshooting calls.
“The basic stuff involves cleaning and lubricating,” Bailey says. “There’s a lot of equipment up in the elevator machine rooms and in the elevator hoistways that needs to be cleaned and lubricated. Then there’s checking all the safety devices. There’s a couple dozen that need to be checked for proper operation.”
Zomchek says that by having a regular, on-site preventative maintenance program, it will save money in the long run.
“It provides a higher level of reliability by addressing issues before they result in shutdowns, it extends the service life of the elevator by replacing or repairing parts before they cause additional wear on other components and it allows for better financial planning by smoothing expenses rather than incurring unplanned repairs,” he says.
Staying on top of elevator maintenance should be a priority at all times, but it becomes even more important in buildings with disabled or elderly residents. Even minor malfunctions can cause serious problems for those who can’t make it up the stairs.
“Let’s face it, if you step into an elevator and it runs to the next floor without any surprises, you are a happy camper,” Malik says. “When the car jerks and makes noises and all of a sudden it goes down and your stomach comes up to your throat, those are the things people hate.”
Problems Arise
The “3 x 5 Rule,” which refers to a maximum distance in inches between the exterior doors and the interior line of the hoistway and interior door (or gate) that rides with the elevator car is the issue that most condos may experience if something goes wrong.
There can also be problems with doors closing, the elevator not leveling off properly, intercoms shorting out and other repairs.
“The most common thing that will shut elevators down is a problem with the doors,” Bailey says. “The doors have electrical switches on them so they need to be closed and locked before the elevator can run. If you get garbage or gravel or other stuff in the sills, it can stop the doors from closing and the elevator from running.”
To rectify this, a condo’s staff can vacuum the area and make sure that it’s clean at all times.
Lights going out is also a situation that scares people into thinking there’s a problem with an elevator and that’s something that a staff member can do if it’s not part of the maintenance program.
Aside from those concerns however, a building’s maintenance staff should stay away from doing even minor repair work on any elevator.
“You hear the horror stories where building maintenance guys have looked at things and had body parts chopped off,” Malik says. “We went to four years of school and on-the-job training, and we had to get licensed in order to understand the safety issues and mechanic issues. We can go up to the machine room where it’s safe and do our work and can get that elevator fixed and running again. It’s a big no-no when people who are not licensed. People are way out of their realm if they think they can fix this.”
Keith Loria is a freelance writer and a frequent contributor to The Chicagoland Cooperator.
Leave a Comment